Hello all -
As reported, Domino and I arrived safe in Monterey on Tuesday, roughly 48 hours after loosing the rudder.
First of all I need to express my gratitude to the Captain and crew of the Coast Guard cutter Hawksbill. Absolutely outstanding professionalism and persistence in some very testing conditions are the reason both I and Domino are both back. I am well aware that their mission priority is to save lives, not property, and will be forever grateful that their training, professionalism and determination brought both of us home in one piece. I'll probably never be able to adequately express this in words, so I will simply keep it at Thank You... and if I ever run across anyone in the service socially the first round is on me, for life.
I pulled most of my gear off Dom on Wednesday, and hauled her with the Travel lift in Monterey. She is currently resting on the hard while I formulate plans for a new rudder fabrication. If all goes well, I hope to bring her home on her own bottom sometime in the next 3-4 weeks, once the new blade is made and installed. Still some things to iron out about the specifics, so the timeframe is somewhat variable for now.
So, what failed? I am of course well aware that Domino is a 30 year old ULDB, and had gone to some pains to thoroughly go over the appendages. I replaced the worn rudder bearings a year ago, and at that time, while the rudder was out of the boat, had the blade tap sounded, moisture metered and ultra-sounded. Unfortunately, what we were looking for was moisture and corrosion, and the blade came up clean on both counts.
What I unfortunately did not look for was piss-poor engineering of the internal structure.
I should qualify the previous and following by saying that I am neither a Marine Surveyor, Naval Architect, Metal Fatigue Expert nor Structural Engineer; I do however have extensive metal fabrication experience, and deal professionally with structural steel specification and fabrication regularly.
And I really did stay at a Holiday Inn Express the other night in Monterey
Now that the pesky layers of fiberglass and foam have been removed by mother ocean, it is pretty evident why the internal structure failed.
I have attached a few pictures of the stub of rudder post that remains [those that are interested and/or more expert are welcome to examine it, I have the post in my garage].
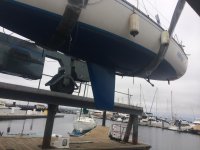
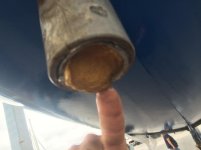
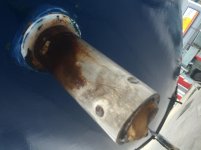
The failure is not IMHO rooted in the fabrication, nor as near as I can tell in hidden corrosion.
Rather it is baked into the engineering [NB: I do not have the original builders spec. and cannot say if this was a choice by the designer or the builder]
As opposed to what I understand to be modern standards, which favor a solid rudder stock running through the entire [or near to it] blade, the rudder stock only extended 6" into the blade. From there it appears that the bottom of the solid SS stock had a blind hole machined into it and a smaller diameter tube inserted and plug welded in 4 places about 1" up from the bottom of the rudder stock. This likely was the end of the armature to hold the foam and fiber glass build up of the blade, given that there is a bit of foam remaining on the inside of the tube.
What that joint creates is 3 big problems structurally:
First, because they are 2 separate pieces of metal any "tolerance" in the machining, even minute, will translate into slop as the joint is loaded.
Second, because the plug welds are at the top of the joint, they will create a nifty pivot point for the slop to lever from.
Third, because the wall of the inserted tube is thinner and likely weaker than the remaining wall of the stock, as the joint is fatigued over time the stronger outer "tube" will end up being a shear point.
With the benefit of hindsight, I now am convinced it was probably only a matter of time before the rudder failed.
It's an unfortunate way to end this adventure, and certainly not what I anticipated.
If you have an older rudder I would encourage anyone to examine it not only for moisture and corrosion, but how it was built and engineered in the first place.
Let's face it, we know a lot more now than back then about how things should be done.
So, that's what I know to date.
My Fourth of July will be a little different than I anticipated, and will be spent dodging the extensive arsenals of my neighbors in West Oakland instead of under a kite in the middle of the ocean.
I'm not complaining, not by any means.
Domino and I will be back sailing soon enough. And 2016 is right around the corner.
Thank you all for your support, condolences and help.
And of course, hat off and three heartfelt cheers to the Capt & Crew of USCGC Hawksbill.
Standing by Oakland
Dave Herrigel
SV Domino
As reported, Domino and I arrived safe in Monterey on Tuesday, roughly 48 hours after loosing the rudder.
First of all I need to express my gratitude to the Captain and crew of the Coast Guard cutter Hawksbill. Absolutely outstanding professionalism and persistence in some very testing conditions are the reason both I and Domino are both back. I am well aware that their mission priority is to save lives, not property, and will be forever grateful that their training, professionalism and determination brought both of us home in one piece. I'll probably never be able to adequately express this in words, so I will simply keep it at Thank You... and if I ever run across anyone in the service socially the first round is on me, for life.
I pulled most of my gear off Dom on Wednesday, and hauled her with the Travel lift in Monterey. She is currently resting on the hard while I formulate plans for a new rudder fabrication. If all goes well, I hope to bring her home on her own bottom sometime in the next 3-4 weeks, once the new blade is made and installed. Still some things to iron out about the specifics, so the timeframe is somewhat variable for now.
So, what failed? I am of course well aware that Domino is a 30 year old ULDB, and had gone to some pains to thoroughly go over the appendages. I replaced the worn rudder bearings a year ago, and at that time, while the rudder was out of the boat, had the blade tap sounded, moisture metered and ultra-sounded. Unfortunately, what we were looking for was moisture and corrosion, and the blade came up clean on both counts.
What I unfortunately did not look for was piss-poor engineering of the internal structure.
I should qualify the previous and following by saying that I am neither a Marine Surveyor, Naval Architect, Metal Fatigue Expert nor Structural Engineer; I do however have extensive metal fabrication experience, and deal professionally with structural steel specification and fabrication regularly.
And I really did stay at a Holiday Inn Express the other night in Monterey

Now that the pesky layers of fiberglass and foam have been removed by mother ocean, it is pretty evident why the internal structure failed.
I have attached a few pictures of the stub of rudder post that remains [those that are interested and/or more expert are welcome to examine it, I have the post in my garage].
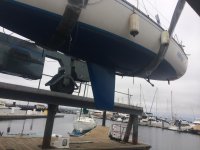
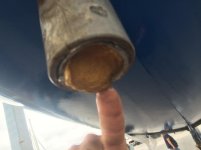
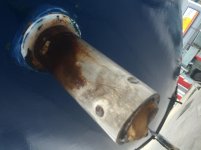
The failure is not IMHO rooted in the fabrication, nor as near as I can tell in hidden corrosion.
Rather it is baked into the engineering [NB: I do not have the original builders spec. and cannot say if this was a choice by the designer or the builder]
As opposed to what I understand to be modern standards, which favor a solid rudder stock running through the entire [or near to it] blade, the rudder stock only extended 6" into the blade. From there it appears that the bottom of the solid SS stock had a blind hole machined into it and a smaller diameter tube inserted and plug welded in 4 places about 1" up from the bottom of the rudder stock. This likely was the end of the armature to hold the foam and fiber glass build up of the blade, given that there is a bit of foam remaining on the inside of the tube.
What that joint creates is 3 big problems structurally:
First, because they are 2 separate pieces of metal any "tolerance" in the machining, even minute, will translate into slop as the joint is loaded.
Second, because the plug welds are at the top of the joint, they will create a nifty pivot point for the slop to lever from.
Third, because the wall of the inserted tube is thinner and likely weaker than the remaining wall of the stock, as the joint is fatigued over time the stronger outer "tube" will end up being a shear point.
With the benefit of hindsight, I now am convinced it was probably only a matter of time before the rudder failed.
It's an unfortunate way to end this adventure, and certainly not what I anticipated.
If you have an older rudder I would encourage anyone to examine it not only for moisture and corrosion, but how it was built and engineered in the first place.
Let's face it, we know a lot more now than back then about how things should be done.
So, that's what I know to date.
My Fourth of July will be a little different than I anticipated, and will be spent dodging the extensive arsenals of my neighbors in West Oakland instead of under a kite in the middle of the ocean.
I'm not complaining, not by any means.
Domino and I will be back sailing soon enough. And 2016 is right around the corner.
Thank you all for your support, condolences and help.
And of course, hat off and three heartfelt cheers to the Capt & Crew of USCGC Hawksbill.
Standing by Oakland
Dave Herrigel
SV Domino