I gave George McKay the emergency rudder that I build as a trial run for the Wildcats new primary rudder last year. He's using it on his Capo 30 (modified to 33 feet) "Skye", so I need to make another rudder. The E-rudder I made then was a bit of overkill for an S2 7.9, though according to George, it steered Skye just fine in 10-13 knots of breeze and some swell. It'll go to Hawaii with Skye on the next Pac Cup. That confirms that the basic method works, so here we go again. Skye's rudder had a 15 inch chord and was almost 7 feet tall.
I'm not a big fiberglass guy. I mean...I'm not high-tech. With advice from Greg Nelson, and after borrowing some pumps etc. from him, I vacuum-bagged the Wildcat's primary rudder, and it's tight. Skye's rudder was a dry-run for the primary rudder and I bagged that. It didn't go as well but what I learned from doing that, made the primary rudder better, so it's all good. However, this time, I'm going to do it low tech, no vacuum bagging.
The core of the rudder is 2 x 3 redwood. Why? Because there's a huge pile of 12 and 16 foot pieces of this stuff lying in an empty lot down the street and it's free. I used it for Skye's rudder...it works. this will be smaller than Skye's rudder, so seems good to me. The pictures are deceiving, as I was trying to glue on a piece in the bottom of the rudder, the leading edge to make it balanced. I was using TiteBond II, which has zilch gap-filling ability and it just didn't work. So I knocked it off with two whacks from a hammer and I'm back to a 12 inch-chord, straight blade. That's the four "Main" edge-glued boards in the picture. That will be plenty big enough.
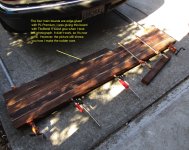
Here's the rudder core, clamped on my driveway, where is where I do all my low-tech work. The glue holding the four remaining pieces, glued up edge-wise, is PL Premium polyurethane construction adhesive. PL Premium is cheap. It gap-fills just great. It's strong as #$%^&*...lots of the DIY boat guy use it for quickie plywood-panel boats. I used to use it to repair cabers for the Highland Games. the wood failed before the PL Premium, ever did. I make up some test joints when I built Skyes e-rudder and tested them. The redwood failed before the joint did.
This rudder is 6 feet tall and will have a 12-inch chord, maybe a scooch more, like 12.5, when I'm done with the fiberglassing.
I'm not a big fiberglass guy. I mean...I'm not high-tech. With advice from Greg Nelson, and after borrowing some pumps etc. from him, I vacuum-bagged the Wildcat's primary rudder, and it's tight. Skye's rudder was a dry-run for the primary rudder and I bagged that. It didn't go as well but what I learned from doing that, made the primary rudder better, so it's all good. However, this time, I'm going to do it low tech, no vacuum bagging.
The core of the rudder is 2 x 3 redwood. Why? Because there's a huge pile of 12 and 16 foot pieces of this stuff lying in an empty lot down the street and it's free. I used it for Skye's rudder...it works. this will be smaller than Skye's rudder, so seems good to me. The pictures are deceiving, as I was trying to glue on a piece in the bottom of the rudder, the leading edge to make it balanced. I was using TiteBond II, which has zilch gap-filling ability and it just didn't work. So I knocked it off with two whacks from a hammer and I'm back to a 12 inch-chord, straight blade. That's the four "Main" edge-glued boards in the picture. That will be plenty big enough.
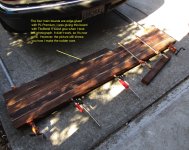
Here's the rudder core, clamped on my driveway, where is where I do all my low-tech work. The glue holding the four remaining pieces, glued up edge-wise, is PL Premium polyurethane construction adhesive. PL Premium is cheap. It gap-fills just great. It's strong as #$%^&*...lots of the DIY boat guy use it for quickie plywood-panel boats. I used to use it to repair cabers for the Highland Games. the wood failed before the PL Premium, ever did. I make up some test joints when I built Skyes e-rudder and tested them. The redwood failed before the joint did.
This rudder is 6 feet tall and will have a 12-inch chord, maybe a scooch more, like 12.5, when I'm done with the fiberglassing.
Attachments
Last edited by a moderator: