OK, I'm just going ahead and making the main rudder trim tab. I bought some stainless steel, and my friend Len S. welded the bits together today. Then I glued up materials from Greg Nelson onto the shaft. This shows the little templates I made to hold the pieces in place while Len worked his TIG magic.
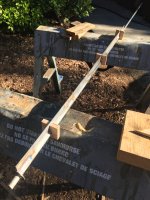
A closeup of the welding. The washer is a "bearing surface". The last 3/4 inch of the s.s. shaft sits in a thin bushing on another piece of stainless at the bottom of the rudder. A couple of nylon washers will separate the foil of the tab, from the bushing area. So thestainless washer takes the very minimal weight of the trim tab. It will butt up next to those nylon washers.
I think this is ridiculous overkill in terms of strength but WTH, right?
Here, I've attached the lastafoam from Greg to the flat stock welded to the stainless rod. PFL Premium polyurethane glue is doing the work...LOVE this stuff.
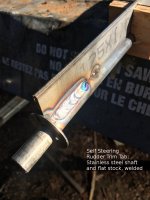
A bit of a close-up. Note the fiberglass rod I've PL-Premium'ed to the stainless steel shaft. that will form the leading edge of the foil. Once the PL solidifies I'll make some epoxy spooge and get it in there to even things out a big and then longboard sand the lastafoam into the foil shape.
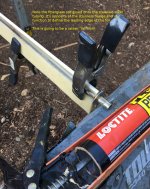
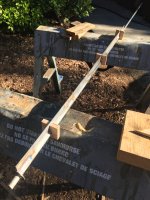
A closeup of the welding. The washer is a "bearing surface". The last 3/4 inch of the s.s. shaft sits in a thin bushing on another piece of stainless at the bottom of the rudder. A couple of nylon washers will separate the foil of the tab, from the bushing area. So thestainless washer takes the very minimal weight of the trim tab. It will butt up next to those nylon washers.
I think this is ridiculous overkill in terms of strength but WTH, right?
Here, I've attached the lastafoam from Greg to the flat stock welded to the stainless rod. PFL Premium polyurethane glue is doing the work...LOVE this stuff.
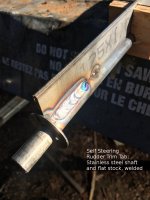
A bit of a close-up. Note the fiberglass rod I've PL-Premium'ed to the stainless steel shaft. that will form the leading edge of the foil. Once the PL solidifies I'll make some epoxy spooge and get it in there to even things out a big and then longboard sand the lastafoam into the foil shape.
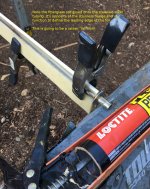