Since it didn't smell like epoxy, being all wrapped up with duct tape 'n all, I put the wrapped vane mast in my study under the ceiling heater vent last night. Today, during a break from work, I pulled off the duct tape and here we are...
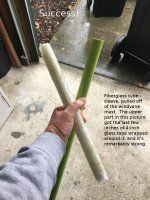
Why did I do this? In fact, why use a fiberglass mast at all? Answer: because I saw that the Mister Vee vane uses a fiberglass mast, and I had it. I know how tough the stuff is, so why not? Anyway, why make the sleeve? Because it's a course-setting system. The whole vane carrier has to rotate on the mast so you can align the course with the prevailing wind, right? Well, that sleeve fits very closely around the mast, enough to not wobble at all, but not so closely that it won't spin easily.
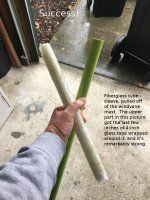
Why did I do this? In fact, why use a fiberglass mast at all? Answer: because I saw that the Mister Vee vane uses a fiberglass mast, and I had it. I know how tough the stuff is, so why not? Anyway, why make the sleeve? Because it's a course-setting system. The whole vane carrier has to rotate on the mast so you can align the course with the prevailing wind, right? Well, that sleeve fits very closely around the mast, enough to not wobble at all, but not so closely that it won't spin easily.