I'm also, sort of simultaneously, working on an emergency rudder. Here are a couple of pictures of my killer woodworking shop. Yes, you can totally be jealous of my driveway. This is the emergency rudder under construction, not my primary rudder. You should see the workshops that most of the guys on the wooden boat forum have. I feel like a real piker when I show my photos over there.
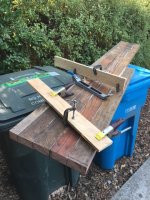
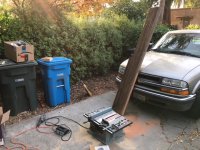
Finally, here's an offcut from the emergency rudder. I tried to torque it apart. The rudder is weathered redwood that's glue'd up with PL100 polyurethane adhesive... NOT epoxy, $6.99/tube Loctite PL100. You'll note that the wood broke before the joint gave up. Admittedly, the wood broke at a weak point near a knot, but still.
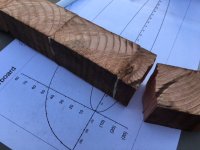
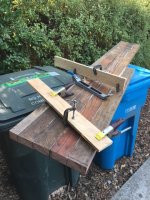
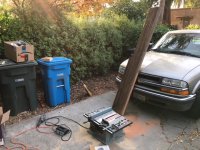
Finally, here's an offcut from the emergency rudder. I tried to torque it apart. The rudder is weathered redwood that's glue'd up with PL100 polyurethane adhesive... NOT epoxy, $6.99/tube Loctite PL100. You'll note that the wood broke before the joint gave up. Admittedly, the wood broke at a weak point near a knot, but still.
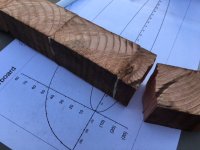
Last edited: