Joan helped me get the rudder in the bag I had for it, after doing all the layup, finding out that I hadn't cut enough triaxial to quite get to the trailing edge on both sides, removing it and laying it all in, again. Here it is, hanging from a line between two sawhorses.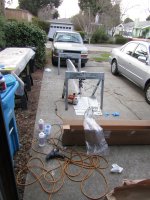
One end of the line is tied to my truck, the other end is tied to some Highland Games weights. There are bolts driven into the end of the rudder, with big washers on them. The bolts/washers fit into loops in the rope, to suspend the rudder off the ground, trailing-edge down.

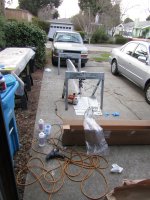
One end of the line is tied to my truck, the other end is tied to some Highland Games weights. There are bolts driven into the end of the rudder, with big washers on them. The bolts/washers fit into loops in the rope, to suspend the rudder off the ground, trailing-edge down.

Last edited: